Continous Bleaching
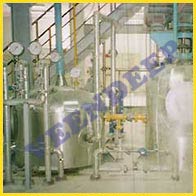
The
main purpose of bleaching is to remove coloring matters by absorption to
obtain finished product with the desired color, on the other hand, for
conventional refining, bleaching serves also to eliminate traces of soap
before oil is passed to the final stage of deodorization.
The degummed/neutralised oil is first heated to desired temperature and
then bleaching earth is added in adequate quantity controlled by PLC into
the OILTEK Oil Earth mixer under vacuum.
This mixture of oil and earth is then pumped to OILTEK Bleacher where it is
agitated by open sparge steam and uniform bleaching takes place.
This is then transferred to Pressure leaf filters where the spent earth (
Cake) is separated and filtered oil again by passing it through polish
filters.
The salient features of the process are as follows:
- Uniform holding time of the oil-earth mixture in the bleacher
- Oil filtration in hermetic leaf filters that requires no
maintenance.
- Savings of both labor and floor space, as well as in a lower
bleaching earth consumption to obtain the same bleaching result.
- Accurate and convenient metering of oil and earth for obtaining
quickly oil of the desired color.
- Filtered oil is kept under vacuum during whole process.
- The bleacher is totally maintenance free as there are no
mechanical agitators.
- Oil content in spent earth (cake) not exceeding 24%.
|